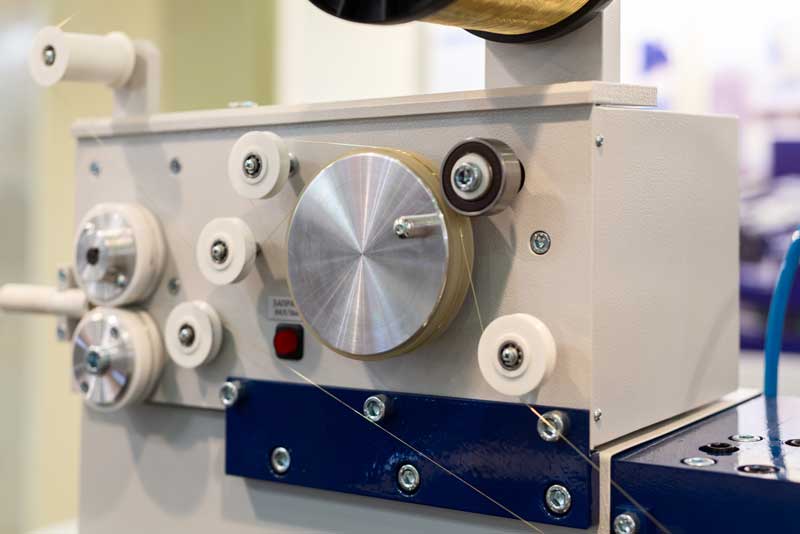
In the ever-evolving landscape of manufacturing, precision and innovation are the keystones of success. Wire Electrical Discharge Machining (Wire EDM) has emerged as a beacon of these qualities, offering an array of benefits unmatched by traditional machining methods. This cutting-edge technology is shaping the future of various industries, including aerospace, automotive, medical devices, and more. Here, we explore the top 10 advantages of choosing Wire EDM for your precision manufacturing needs, illustrating why it's an indispensable tool in modern manufacturing.
- Exceptional Accuracy: Wire EDM stands out for its ability to achieve incredibly tight tolerances, often down to a few micrometers. This precision is crucial in industries where even the slightest deviation can compromise the functionality of a part.
- Complex Geometries: One of the most remarkable capabilities of Wire EDM is its proficiency in cutting intricate shapes and complex designs. This ability makes it invaluable for manufacturing detailed components like turbine blades, custom gears, and other complex parts.
- No Mechanical Stress: The EDM process is non-contact, meaning the wire never physically touches the workpiece. This absence of direct contact eliminates mechanical stresses, reducing the risk of warping or distorting the material.
- Material Versatility: Wire EDM can cut through a vast range of materials, including hard metals such as titanium and softer ones like aluminum. This versatility expands the scope of projects that can benefit from EDM technology.
- Surface Finish Quality: The process naturally results in smooth finishes, reducing or eliminating the need for secondary finishing processes. This not only saves time but also maintains the integrity of the part.
- Cost-Effective for Low Volume: Traditional machining methods often require extensive tooling, which can be cost-prohibitive for small runs. Wire EDM is more cost-effective for low-volume or prototype parts due to minimal tooling requirements.
- Minimized Waste: Wire EDM is efficient in its use of material, typically producing less waste compared to traditional machining. This efficiency is not only good for your budget but also better for the environment.
- Safe for Delicate Parts: The non-contact nature of Wire EDM makes it ideal for machining delicate parts or fragile materials that could be damaged by the forces involved in conventional machining.
- Customization Capabilities: The flexibility of Wire EDM allows for high customization in manufacturing. It can easily accommodate changes in design, making it perfect for bespoke or specialized projects.
- Time Efficiency: Despite the high level of precision it delivers, Wire EDM is relatively fast, especially for complex cuts. This efficiency ensures shorter production cycles, enabling faster turnaround times for projects.
Conclusion:
The top 10 advantages of Wire EDM make it a superior choice for a wide range of precision manufacturing needs. Whether tackling a complex aerospace component, a delicate medical device, or a custom automotive part, Wire EDM offers an unmatched blend of precision, versatility, and efficiency. By choosing Wire EDM for your manufacturing needs, you are investing in a technology that not only meets but often exceeds the rigorous demands of modern production. This commitment to quality and innovation is what sets Wire EDM apart as a cornerstone of contemporary manufacturing excellence.